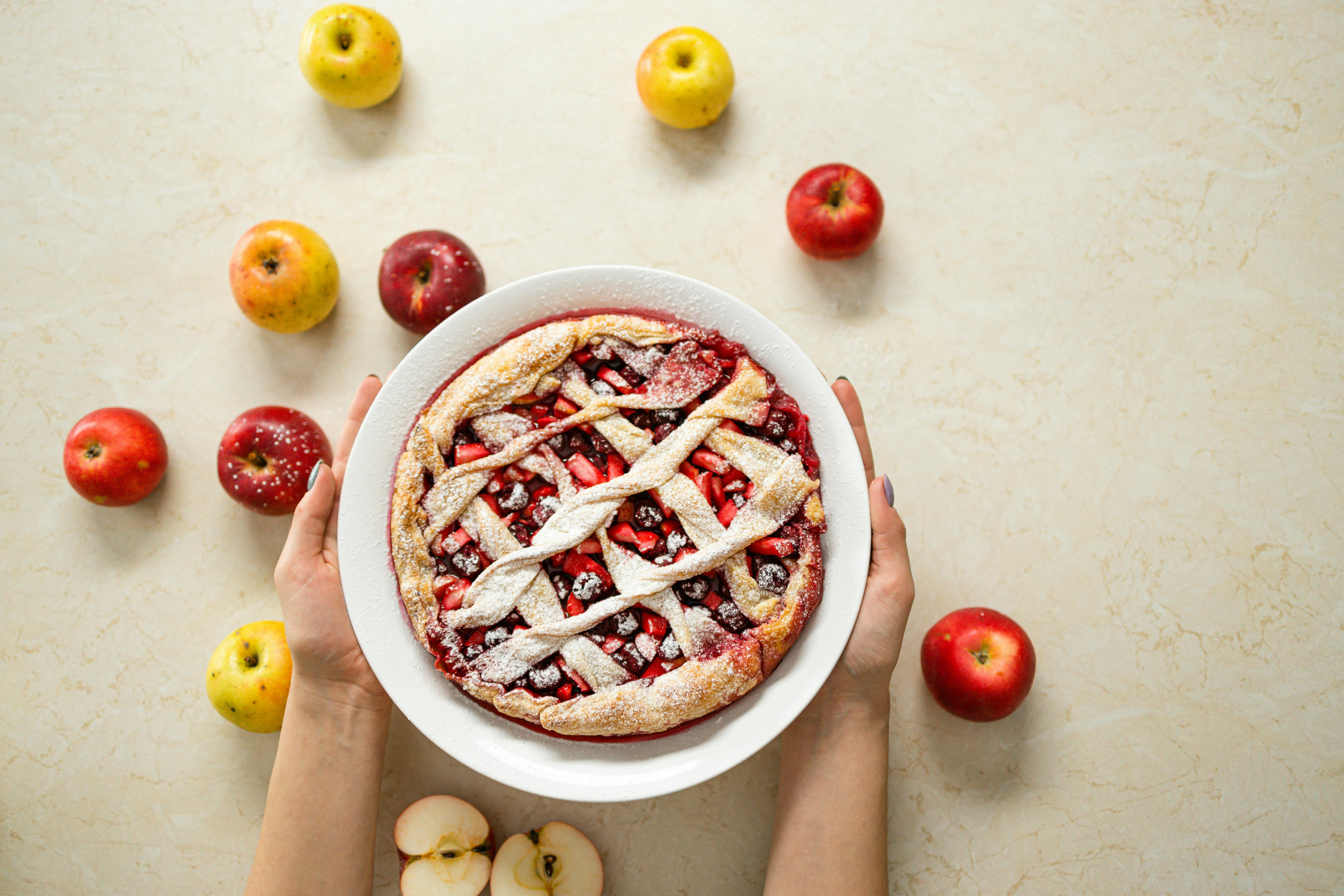
Improved natural fine stone installation system changing the exterior cladding industry
As the popularity and use of Natural Thin Stone grows, research and installation findings are producing improved standards that result in better, longer-lasting installations at reduced costs.
Historically, the minimum acceptable standards for installing Natural Thin Stone have long been as follows:
1. Apply siding over studs. This sheathing can be exterior OSB, plywood, exterior drywall, drywall, or cement board.
two. Staple the construction paper to the siding. Attach the construction paper in horizontal strips. Start at the bottom and overlap 2″ (like shingles). Overlap vertical joints at least 6″. If you are using flashing or support brackets (anchors), install them before continuing to the next step.
3. Screw, staple or nail metal lath to studs with a maximum horizontal gap of 16″ oc. Overlap metal lath by at least 1″ for horizontal and vertical joints. At corners, overlap vertical joints at least 16″ around the corner to prevent corner cracking. Use galvanized spiked nails 6″ o.c. vertically for exterior work or steel wire furring nails 4″ o.c. center for interior work Minimum nail penetration is 1″ on studs. For steel studs, the batten must be anchored with corrosion resistant screws having a minimum shank diameter of 0.190″.
Four. Apply a 3/8″ to 1/2″ thick scratch coat of mortar over the metal lath and embed it. Use a notched scraper, notched trowel, or a small piece of lath to lightly scrape horizontal grooves in the starter layer. Allow the initial layer to cure for a minimum of 24 hours.
In the United States, depending on geography, climate, humidity level, improved installation techniques and systems have been developed that offer superior performance. One such approach is described below.
Improved system for use over wood or steel beam substrates
In this application, the lath and stripe layer is replaced with a cement backer board and a flexible, roll-grade waterproofing membrane. The use of cement backer board eliminates installer errors that can occur from excessive scratching of the initial mortar layer. If this scratch occurs too deep, moisture can penetrate the coating and cause corrosion of the batten and ultimately total failure of the installation system. Through the use of cement backer board and flexible roll-grade waterproofing membrane, this weakness of the lath and scuff coat system is eliminated.
Similar to thin-set tile installations, movement joints are also used every 8 to 10 feet. The graphic below illustrates Laticrete’s approach using its HydroBan acrylic waterproofing membrane and its 255 MultiMax thin-set mortar. This type of system not only offers superior performance, but can also reduce total installed costs by 10% to 30%. Other enhanced products are listed below.
These products have been tested for use in most climates in the United States and have been shown to provide long-lasting protection. Many include guarantees as well.
cement backer board
National Gypsum PermaBase
waterproofing membrane
Laticrete HydroBan
Mapelastic Smart by Mapei
ProSpec Sure-Coat
Mortar
Laticrete 255 MultiMax
Mapei Granirapid Mortar
Prospec StayFlex 590
Other apps
When applying natural fine stone directly over existing concrete, cinder block or masonry, the addition of a roll-grade flexible waterproofing membrane will significantly improve the strength of the installation.
Overall, these improved natural fine stone installation systems improve the quality, longevity, and cost of using the superior natural fine stone cladding product.